With the constant development in the domain of consumer electronics; mainly in terms of technology size reduction. Aluminum Core PCB is becoming more and more popular among PCB manufacturers, predominantly because the use of aluminum-clad PCBs allows the redirection of PCB thermals away from the onboard components. Moreover, Aluminum Core PCB is slowly but surely becoming the only feasible solution to high power and tight tolerance applications. So, in today’s guide, we will go over the design benefits and limitations of using aluminum core PCB technology and the many promising applications associated with it.
Aluminum Core PCB
An Aluminum core PCB contains a dielectric metal base bonded with a copper circuit layer. In order to create superior heat transfer capability, that helps to cool vital PCB components while eliminating problems connected with managing fragile ceramics. They have many other names such as Aluminum base, MCPCB (Metal Clad Printed Circuit Board), IMS (Insulated Metal Substrate), Thermally Conductive PCBs, etc. Their make is basically a thin layer of thermally conductive but electrically insulating dielectric material clad PCBs, laminated between a metal base and a copper foil. The copper foil is etched into the desired circuit pattern and the metal base draws heat away from this circuit through the thin dielectric.
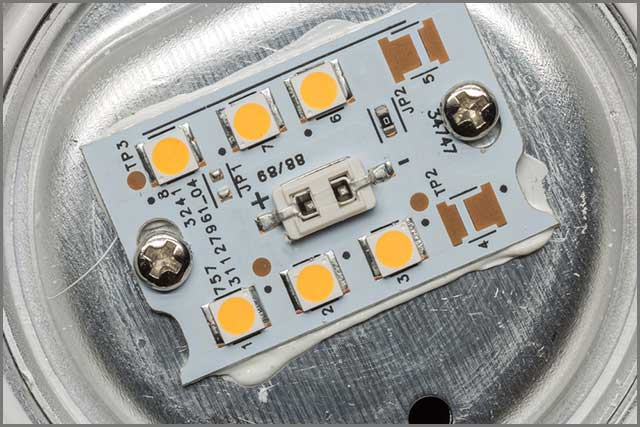
JLCPCB is the foremost PCB prototype & manufacturing company in china, providing us with the best service we have ever experienced regarding (Quality, Price Service & Time).
Design Benefits of Using Aluminum Clad PCBs
1) Great Heat Dissipation
High thermals can inflict severe damage on PCBs and can also ruin delicate on board SMD components. Aluminum substrate PCBs solve thermal dissipation issues, by relocating the heat away from any vital PCB component. Thus, minimizing the harmful effect heat can have on the PCB board.

2) Light Weight
This is one of the biggest advantage of using aluminum PCB. Aluminum is a surprisingly light metal & for it’s light weight it’s extremely resilient. Production of PCBs out of aluminum allows manufacturers to create very light-weight and portable PCBs, without compromising on the structural strength and resilience of the PCB itself.
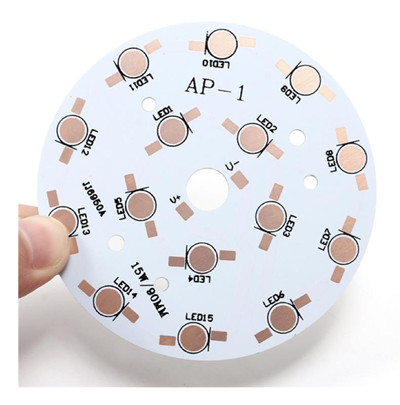
3) Enhanced Durability
Aluminum PCBs last for a significantly longer period of time as compared to their fiber glass or ceramic counter parts. Aluminum is a sturdy base material that reduces the risk of accidental breakage during handling, manufacturing, or everyday use. Also, with proper storage conditions, aluminum PCB boards can maintain their integrity for a long period of time.
4) Economical & Easily Accessible
As a base metal, aluminum is easily accessible in almost every climatic condition. This makes aluminum very easy to mine and refine. Consequently, the manufacturing cost pertaining to aluminum PCB reduces and makes it possible to deliver high quality aluminum PCB builds at a highly affordable cost.
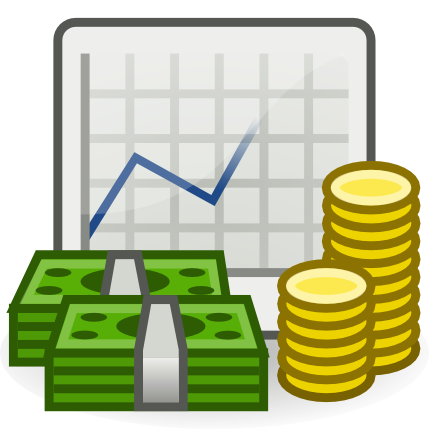
5) Safe For the Environment
Aluminum is a non toxic material, the main reason why its in every household utensil such as spoons and pans. Besides that, aluminum is also recyclable making it highly reusable and safe for the environment. Thus using aluminum in PCB production contributes to the well being of the environment.
6) Dimensional Stability
Aluminum PCBs have larger firmness than other insulating materials. When their temperature rises from 30 °C to 140 ~ 150 ° C, they still stay stable. The dimensional change of the aluminum PCB substrate is only 2.5 ~ 3.0%.

Limitations of Using Aluminum PCBs
When it comes to the design limitations of using aluminum PCBs, there aren’t many. Most of the disadvantages that come with using Aluminum PCB are due to the production process itself and not the material itself. Never the less, some design limitations of using Aluminum PCBs are:
- It is surprisingly difficult to create double layer PCBs using aluminum. The current mainstream in the PCB design market has only managed to do a single layer aluminum PCB effectively.
- Aluminum PCBs sometimes become susceptible to pressure and electrical strength issues, though by only a small margin.
Applications of Aluminum Core PCBs
1) Solid State Relays
Aluminum PCB boards are used in designing solid state relay. Since, they feature a very thermally efficient and mechanically sturdy PCB substrate to reallocate heat away from critical relay components.
2) Consumer Electronics
The portability and lightweight of Aluminum core PCBs allows them to serve in designing consumer electronic products such as control lighting, interior building lighting fixtures, and camping gear, etc.
3) LED Circuit Boards
The usage of an aluminum substrate in LED PCBs guarantees the minimum possible operating temperatures and maximum brightness, color, and operational life.
4) Power Conversion Circuit Boards
Aluminum clad PCBs offer a wide range of thermal operating temperatures. This makes them ideal to be used for high power conversion boards such as DC-AC adapter, stabilizer, etc.
5) AC/DC Motor drives
Aluminum clad PCBs are commonly used in AC/DC motor driver boards, as they provide the electrical isolation needed to meet the set operating conditions and safety test requirements.
6) Audio & Radio Equipment
Due to their capability of redirecting heat away from sensitive on board parts. Aluminum core PCBs are commonly used in audio equipment such as mixers and preamps, allowing them to be used for longer periods of time under high audio gain stress.